Brake Hoses
Definitely replace front and rear brake hoses with stainless
steel, teflon lined type (Moss Part # 182-228).
Brake Rotors We do not recommend re-machining brake rotors. OEM thickness (0.345")
should be maintained where possible. If you must re-machine (0.300" minimum
thickness) your old brake rotors then they should be non-directional finished,
simply machining the brake rotors the conventional way will result in a
directional finish much like that of an old gramophone record, this type of
finish will promote glazing and brake pad squeal. Be sure that the brake rotors
are hand finished (usually 40-60 micro-inch) with No 120-grit sandpaper.
In 1994 British Automotive introduced angular
grooved brake rotors, we continued to sell these into 1996, at that time we
re-evaluated the situation and concluded that, besides serving as a brake pad
wear indicator, that by simply machining a channel in the brake pad we could
achieve the same results. During 1998 we were in a position to further evaluate
this procedure and found, upon examination, that the channel in many of the
brake pads, which we had previously installed, had become blocked over time
with brake pad material. The more brake pad wear that was evident, the more the
channel was blocked with transferred pad material.
Based upon the above, we have reintroduced
brake rotor set part # BTB387/DG. The DG standing for "directional groove". Our
original DG brake rotors had 6 grooves machined on both sides of each brake
rotor. Current DG brake rotors have 4 grooves per side. These "Brembo" rotors
are surface ground to 60 micro-inch. FYI the MGB factory workshop manual
specifies that brake rotors be surface ground to 63 micro-inch. I have seen 3
methods of reading surface finishes: RA (roughness average), RMS (roughness
mean surface), and AA (average area) all expressed in micro-inches. To convert
RA to RMS multiply RA by 1.11. That is all I know.
These angular grooves are essential when
using today's modern brake pads. They allow gas buildup, between the brake pad
and rotor, to escape, as well as channeling away water, brake dust and debris.
This kind of brake rotor is preferred over the cross-drilled type brake rotor.
The brake pad channel is still retained, with its primary function serving as a
wear indicator. |
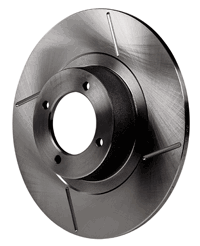 |
We would now like to present more information on MGB brake
pad choices for both Street-Street Performance and Racing.
First of all, brake pads containing asbestos
are a thing of the past. I only mention them here as a reminder of their past
performance, rather like a belated obituary.
Brake pads containing asbestos were capable
of absorbing lots of heat without burning, however, they would begin to glaze
as low as 250 degrees F, thereby reducing their coefficient of fiction (COF),
and as temperatures reached 350 degrees F, fading would become apparent.
Sustained high temperatures would form a glaze deep enough into the pad
material that they would, in many cases, never recover. On top of this we knew
how inefficient this material became when wet. It is estimated that asbestos
brake pads under these conditions lost almost 2/3 of their COF. "May they rest
in peace."
We don't know how lucky we were (back in the
early 60s) having OEM front brake disc systems on both the MGA and MGB as
standard equipment. Numerous vehicle manufacturers offered this set up as an
optional sports extra, while others continued on with regular brake drum
systems well into the early 70s. Next time you are into replacing the front
brake pads on your MGB, please don't compromise; use a quality brake pad
set.
The modern performance brake pad choices of
today are: 1) Carbon Metallic (a registered trademark of "Performance
Friction Corporation"), 2) Carbon Kevlar, 3) Hawk Ferro Carbon
(formally known as Carbotic), and 4) Ceramic.
British Automotive exclusively promotes and
sells Carbon Kevlar RS-4 compound brake pads. With many years of sales
and feedback from customers, we have decided to offer this brake pad material
as the only choice. If you decide that you would prefer a different brake pad
compound, you will have to contact one of the appropriate companies mentioned
below.
WHAT IS CARBON METALLIC
®?
1-Carbon Metallic is "Performance Friction
Corporation's brand name for its brake pads. These are completely different
from organic or semi-metallic pads. They offer superior braking pedal feel and
longer life without fade at high temperatures. As the name implies, they are of
Carbon Metallic composition as opposed to being organically based. Carbon
Metallic contains no asbestos, no kevlar and no lead. Organic and semi-metallic
pads use clay as a filler to cut costs which sacrifices performance.
WHAT MAKES CARBON METALLIC BETTER THAN
OTHER BRANDS?
Carbon Metallic brake pads meet Federal Motor Vehicle
Safety Standard 105. Not all brake pads on the market meet these stringent
standards. They are also Original Equipment on over 2,000,000 Ford and GM
vehicles. Carbon Metallic is the safest pad you can buy. They are
integrally molded using Ionic Fusion system and have the highest shear strength
in the brake industry. Carbon Metallic pads are completely ABS
compatible. A significant feature of Carbon Metallic pads is that brake
force remains consistent throughout pad life.
CAN I TELL THE DIFFERENCE WHEN USING
CARBON METALLIC?
Performance Friction Carbon Metallic pads are
extremely strong, which offers superior brake pedal feel. Less strong
organic/organic based or semi-metallic pads actually can compress especially
when hot. Carbon Metallic pads continue to grip even when hot, offering
consistent braking and pedal feel. There is no good, better or best grade.
There is only one Carbon Metallic. This strength also makes Carbon
Metallic more compatible with ABS.
ARE CARBON METALLIC PADS
NOISY?
Carbon Metallic pads are manufactured to the highest
standards from the raw material to the finished product. With a well-maintained
system, i.e., properly actuating calipers and brake rotors that are in spec.,
Carbon Metallic should not make noise.
ARE CARBON METALLIC PADS HARD ON BRAKE
ROTORS?
No! In fleet use many users such as Federal Express, Pepsi
Cola, Penske Truck, etc. have drastically reduced their rotor replacements.
Rotor wear is reduced with Carbon Metallic pads.
PERFORMANCE FRICTION Z-RATED
COMPOUND?
The highest friction brake pads available for street
vehicles, for customers who demand ultra high performance braking with low
wear, rotor compatibility and fade resistance. Ideal for the driver who demands
maximum friction while maintaining excellent everyday street use.
Performance Friction Z-rated High
Performance Glycol Based Brake Fluid is an excellent replacement to OEM
fluids with a dry boiling point of 550 degrees F. It has extremely low
compressibility and excellent lubrication properties. Z-rated fluid is
non-corrosive to brake system components and has been proven to be easier on
both natural and synthetic rubber seals. Z-Rated Brake Fluid (16oz steel
container). The preceding information is courtesy of "Porterfield Enterprises
Ltd."
For the MGB we recommend the Z-Rated Compound
with a COF in the low 40s. Operating temperatures for this compound are not
published and there is no thermal heat barrier between the friction material
and backing plate. Therefore, we recommend the use of Z-Rated Brake
Fluid with these pads. Contact "Porterfield Enterprises Ltd." at
(949)(949) 548-4470548-4470 for brake fluid and brake pads with this compound.
The recommendation is for the use of non-directional finished brake rotors,
60RMS or smoother.
CARBON KEVLAR
2-Carbon Kevlar R-4. A uniquely engineered composite
brake pad. This precision design combines Kevlar, Carbon and an array of other
high performance materials to make a better brake pad. R-4 Carbon Kevlar is a
high COF material 0.485 and incorporated in its design a unique ceramic heat
shield integrally molded and designed specifically for high temperature
applications (75F to 1500F) to minimize heat transfer. NOT
"PRE-BURNISHED."
R-4S: Street High-Performance &
Limited Competition. Slightly different compound than R-4. This is the high
performance street pad of choice. Very high COF 0.41. No dust*. No squeal
(depends on brake disc condition and RMS finish). This is the fastest stopping
road pad available (I definitely agree with that statement). Temperature limits
75 F to 1050 F. Thermal heat barrier designed. "PRE-BURNISHED."
R-4E: Endurance Racing Pads with Longer
Life. This endurance pad, with special formulation for long races, runs
cool and wears longer than our regular R-4. COF 0.475 Temperature limits
75F to 1350F. Great for extended time events. NOT "PRE-BURNISHED"
Thermal heat barrier design. The preceding information is courtesy of
"Porterfield Enterprises Limited" and edited for applicable
content.
* Note: All brake pads emit dust as they
wear. Lighter material colors are not as noticeable. Brake dust also has a
tendency to adhere to aluminum/alloy wheels more readily and, if not washed
from the wheel, will destroy the wheels finish. British Automotive can supply
you with the following brake pads in R-4S compound only.
* Part # LD48/KEV.Designed for the
factory MGB GTV8 brake caliper assembly, however, they will fit directly into
the MGB brake caliper. This oversize pad gives approximately 20% more swept
area than the OEM size.
* Part # MGB/KEVLAR. British
Automotive custom brake pad. Specifically, designed for the MGB brake caliper
with the largest pad size possible. Greater swept area than LD48/KEV.
HAWK FERRO
CARBON
3- Hawk Ferro Carbon. A Carbon-semi-metallic material
offering high torque, low wear and excellent brake disc life. Carbotic
materials exhibit stable COFs under hot and cold applications.
Black Y5 Compound. Medium torque and
excellent stopping power with extra fade resistance. Provides good pad wear and
is brake disc friendly. Recommended for low temperature applications. 200F to
900F. Vehicle weights 2400# or less. High COFs under cold and hot
applications.
Blue Compound, HAWK 9012. High torque
with superior stopping power. Will not fade. Provides excellent wear and
braking at high temperatures 100F to 1000F. Slightly less brake rotor friendly
than black compound. Recommended for all heavy brake applications with vehicle
weights of 2,400 lbs. to 2,800 lbs. High COFs under cold and hot
applications.
HPS. Street replacement high torque
pad with temperatures of 75F to 700F. High COF, low dust, brake rotor friendly
and silent running.
HP+. Street performance and Rally
replacement much higher torque pad with temperatures of 100F to 800F. High COF,
Dustier than HPS and brake rotor friendly. Ideal for the fast street
driver.
It is recommended that the MGB brake rotors
with their OEM 0.345" thickness be replaced rather than re-machined. The
minimum thickness regrind is set at 0.300" a 0.045" difference.
When installing new Hawk brake pads
and new brake rotors together as pairs, it is OK to use swirl finished rotors.
However, if you ignore the recommendation about installing new brake rotors and
decide that it is cheaper to have them re-machined, then they must be
directionally cut with the surface finish being as smooth as possible, the
emphasis being on smoother the better. Most Hawk brake pad compounds are
"PRE-BURNISHED", however should additional burnishing be required for a
particular compound, instructions will be supplied with the brake pad
set.
Also, Removing brake pad material build-up on
used brake rotor surfaces when changing compounds or brands of brake
pads will assure the proper transfer of friction material on to the brake disc
surface and increase the performance and wear life of both brake pad and brake
rotor.
OEM sized brake pad no thermal heat barrier
Part# HB132 (Black Y5 or Blue Compound)
OEM sized brake pad with thermal heat barrier
Part# CT27TE (Blue Compound) The preceding information is provided
courtesy of "CARBOTECH Engineering" and edited for applicable content.
Please contact them at (954) 493-9669 for brake pads using these
materials.
CERAMIC
4- Ceramic. Ceramic filled brake pads are one of the newest
friction materials being marketed. At the moment I know of no company offering
this material choice for the MGB.
Ceramic based pads contain no steel wool or
fibers. Instead, ceramic fillers and copper fibers are used to handle higher
operating temperatures. Reported to be quieter, more durable, kinder (less
abrasive) to rotors and almost dust free. However, all brake pads generate dust
as they wear. With the light color of the materials used in this type of pad,
brake dust is less visible.
The above information is provided courtesy of
"IMPORT CAR"February 2000 issue and edited for applicable
content.
NOTE: NO CLAIMS RELATING TO WEAR RATES CAN
BE MADE FOR ANY GIVEN TYPE OF BRAKE PAD.
BRAKE PEDAL
MODULATION
Due to the better bite characteristics of modern brake pad
materials, brake pedal modulation becomes of primary concern. With larger pad
areas and higher coefficient of friction materials, the driver should be aware
that front wheel lockup can occur more rapidly if proper pedal techniques,
under heavy braking, are not applied.
REAR BRAKE LINING
MATERIAL
For more effective rear braking, other than installing
larger diameter wheel cylinders, the rear brake lining material can be updated.
Presently we have brake shoe sets available lined with the R-4S compound
PART # ES437/KEV @ $150.00 (not cheap). However, for street and street
performance driving, we have found that the regular brake shoe replacement
lining materials, supplied by various Vendors, when used in conjunction with
upgraded brake pads, to be more than adequate.
Be sure to have your rear brake drums
machined when changing rear brake shoes. To make sure that the brake drum is
machined concentric, we use regular road wheel hubs from the tube axle MGB,
with the brake drum attached. This setup requires Volkswagen brake drum
adapters for machining. OEM brake drum size is 10" with a maximum oversize
regrind set at 10.060"
BRAKE FLUIDS
What is the difference in brake
fluids?
The most popular types of brake fluid are
DOT3 and DOT4, both of which are inexpensive and readily available. Appearing
clear to amber in color, DOT3 is a polyglycol fluid; DOT4 can often be a
polyglycol, as well. These fluids cause rubber parts of the brake system to
swell slightly, improving sealing and preventing leaks. Drawbacks include their
high affinity for moisture, causing both a reduction of the boiling point as
well as rust and corrosion in the brake system. Also, they have a higher
viscosity at low temperature.
Recognized by their purple color, DOT5 fluids
are typically silicone-based products, with extremely high boiling points, and
have no affinity to moisture. DOT5 fluids are more expensive than polyglycol
brake fluids. Due to their air retention properties DOT5 fluids make bleeding
air from the braking system more difficult than DOT3 or DOT4 fluids. For this
reason, DOT5 fluids cannot be used in ABS systems.
Hydraulic system mineral oil (HSMO), a blend
of mineral oil and additives, is easily identified by its green color. This
rare fluid is typically the most expensive. HSMOs have the highest boiling
points and do not contribute to rust or corrosion. However, HSMOs are not
compatible with silicone-based or polyglycol fluids.
Although developed for the consumer market,
DOT4 brake fluid has found wide usage on the NASCAR racing circuit for its high
boiling point (446 degrees F) and increased corrosion resistance.
We continue to use Castrol LMA. However,
regardless of the type of brake fluid used, proper maintenance is the key to
ensuring your brakes operate properly when you need them. It is recommended
that the brake fluid be flushed out and changed at one to two year intervals.
Always keep your brake master cylinder fully topped up.
Brake fade. Brake fade in
association with a firm brake pedal, especially under heavy braking, and with
increasing brake pedal pressure, is usually the result of glazed brake rotors
and or brake pads, either of these two conditions reduces the friction that is
required between the brake pads and brake rotor to effectively bring the
vehicle to a stop within a reasonable distance. However, we have found numerous
MGBs that have had the following: Seized rear brake wheel cylinders, collapsed
front brake hoses, hydraulic problems within the brake master cylinder, and
seized brake caliper pistons (normally a retraction problem)
All of the above increase brake pedal
pressures, relative to stopping the vehicle within a reasonable distance. So be
sure to check these items out first.
Brake pedal fade. This condition
is a hydraulic related problem with either brake fluid loss, the inability of
the brake master cylinder seals to maintain hydraulic line pressure or even
brake fluid "boiling".
|